Экструзионно-выдувное формование
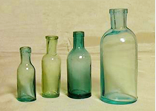
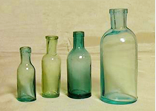
Расплавленный полимер раздувается воздухом и остывает на холодных стенках пресс-формы. В другом случае - инжекционно-выдувного формования (ИВ) (рис. 1, в) - сначала методом литья под давлением изготавливают заготовку в виде пробирки - преформу. Преформу нагревают до состояния эластичной резины, помещают в пресс-форму и в резиноподобном состоянии раздувают сжатым воздухом. Далее готовое изделие остывает на холодных стенках пресс-формы. Исторически экструзионно-выдувное формование бутылок возникло раньше второго способа. Однако в последнее десятилетие метод инжекционно-выдувного формования значительно потеснил первый, и даже некоторые крупные фирмы прекратили выпуск оборудования для экструзионно-выдувного формования. Но в самое последнее время, буквально в последние год-два, наблюдается резкий рост интереса к этому методу производства пластмассовых бутылок. Статья представляет собой попытку объяснить, почему это происходит. Каковы особенности и области применения этого метода и каковы тенденции развития производства бутылок из пластмасс методом экструзионно-выдувного формования в России.
Введем коэффициент капитальных затрат (ККЗ) - отношение стоимости оборудования к его часовой производительности. При близкой цене сырья и прочих равных условиях оборудование окупается тем быстрее, чем выше его производительность. Десять лет назад полиэтилентерефталат (PET) - полимер, из которого делают подавляющее количество преформ, стоил в 5 раз дороже полиэтилена, полипропилена и других полимеров, и поэтому тогда большинство бутылок из полимеров производили методом экструзионно-выдувного формования. Но именно тогда были удешевлены методы синтеза PET и построены мощные заводы по его производству. Машиностроители отреагировали мгновенно - сразу же началось производство оборудования для литья преформ и выдува бутылок из PET.
Эти высокопроизводительные агрегаты способны производить до 40 тыс. преформ в час и выдувать в час до 24 тыс. бутылок. Коэффициент капитальных затрат в случае выдува бутылок из преформ стал ниже, чем ККЗ для экструзионно-выдувного формования. Четыре-пять лет назад началось интенсивное развитие производств ИВ и в России. Построено несколько мощных заводов по производству преформ. Из-за дешевизны рабочей силы в России выгодно поставить пять-шесть очень дешевых полуавтоматов для выдува, чем один дорогостоящий автомат. Поэтому быстро возникли фирмы - производители таких полуавтоматов. Крупнейшая из них - "Продвижение". Но, как правило российский потребитель приобретает один выдувной полуавтомат со средней производительностью выдува 600 бутылок в час.
Эта величина соответствует средним показателям производительности экструзионно-выдувных агрегатов. По коэффициенту капитальных затрат оборудование такой мощности для ЭР проигрывает аналогичному оборудованию для ИВ в 1.5 -2 раза, но этот недостаток сторицей окупается благодаря более широким возможностям метода ЭР. Для того, чтобы аргументировать это утверждение, рассмотрим более подробно процесс выдува бутылок методом ЭР в сравнении с методом ИВ (рис. 1).
Рис. 1, а. Схема экструзионно-выдувного формования: 1 - пресс-форма; 2 - трубная головка; 3 - трубная заготовка
Рис. 1, б. Схема получения трубной заготовки: 1 - тело трубной головки; 2 - мундштук; 3 - дорн; 4 - трубная заготовка
Рис. 1, в. Схема инжекционно-выдувного формования: 1 - пресс-форма; 2 - преформа; 3 - шток
Рис. 2. Способы экструзионно-выдувного формования: а - выдув сверху; б - выдув снизу; в - выдув иглой
Самым существенным является то, что полимер при выдуве бутылок разными методами находится в разных физических состояниях. При методе ЭР - это жидкость, а при ИВ - резина. Это означает, что в первом случае деформация заготовки пластическая - давление раздува невелико, и проработка мелких деталей бутылки - бордюров, логотипов, ребер и т.п. - очень четкая. Когда бутылку формуют из преформы деформация заготовки упругая, для качественного выдува требуется значительно большее давление, и проработка деталей затруднена и, как правило, значительно хуже. Однако замороженные на холодной поверхности пресс-формы обратимые упругие деформации (подобно напряженному железобетону) делают полимер значительно прочнее. Метод ИВ незаменим, если требуется высокая прочность бутылки, например, при розливе высокогазированных жидкостей.
Инжекционно-выдувное формование бутылок имеет более низкий коэффициент капитальных затрат по сравнению с методом ЭР, если пользователь закупает преформы у фирм, специализирующихся на их производстве. Это очень крупные фирмы, имеющие дорогостоящее специализированное оборудование, каждая единица которого выпускает один определенный тип преформы. Особенности процессов литья преформ и последующего выдува из них бутылок накладывает существенные ограничения на величины толщин стенок заготовки, а следовательно, и бутылки.
Между тем регулирование толщины бутылки в методе ЭР достигается очень просто.
Рассмотрим получение трубной заготовки (рис. 1, б). Расплавленный полимер 4 выдавливается экструдером в зазор между мундштуком 2 и дорном 3 трубной головки 1. Дорн можно перемещать относительно мундштука, тем самым меняя величину конусного зазора, т.е. толщину заготовки. Более того, представьте себе, что нужно изготовить бутылку в форме гитары - широкую снизу и узкую вверху. Современные экструзионно-выдувные агрегаты имеют специальный привод для программного перемещения дорна в цикле выдавливания рукава при производстве бутылки. В нашем примере дорн сначала поднят - толщина рукава велика, затем дорн опускается и толщина рукава уменьшается. Таким способом можно достичь высокой степени равнотолщинности изделия. А как добиться равнотолщинности при производстве плоской бутылки с большим отношением большой и малой сторон? Преформы всегда симметричны относительно оси штока 3 (рис. 1, в), поэтому методом ИВ поставленная задача не решается.
В случае ЭР все гораздо проще: пару дорн - мундштук изготавливают с необходимым зазором эллиптической формы. Замена всего двух простых деталей позволяет изготавливать бутылки плоской формы с любым соотношением большой и малой сторон. Еще одно преимущество: только методом формования из расплава возможно производство бутылок с ручками. Для того, чтобы этого добиться в методе ИВ, Необходимо изготовить бутылку специальной формы, отдельно произвести ручку методом литья под давлением и вставить ручку в бутылку. В этом случае, конечно, и ККЗ, и накладные расходы, значительно выше, чем в методе ЭР.
Список достоинств метода экструзионно-выдувного формования по сравнению с методом инжекции с раздувом можно продолжить, но и перечисленного достаточно, чтобы понять - методы дополняют друг друга. До последнего времени в России разливали главным образом газированную и негазированную воду, а также напитки на ее основе. Сейчас стало выгодно разливать и другие жидкости. К нам обращаются представители торговых фирм, которые до сих пор завозили уже расфасованные в бутылки товары из-за рубежа. Стало выгодным развивать собственные химические производства на базе имеющихся и самим фасовать произведенные жидкости в бутылки. Это автомобильная косметика, шампуни, жидкости для мытья посуды и другие товары бытовой химии, соки, лаки, краски и т.п. Новая для России номенклатура продукции требует большого количества и разнообразия тары по объему, форме и материалам, из которых бутылка изготавливается. Это и есть причина, по которой метод экструзионно-выдувного формования емкостей переживает в России второе рождение.
Особенно важен выбор материала, из которого изготавливают бутылку. В таблице даны оценки основных технологических и эксплуатационных свойств полимеров, применяемых для изготовления полой тары. Сравнение проведено по пятибалльной системе - от пятерки - отлично, до единицы - очень плохо.
Конечно, было бы хорошо выдувать все бутылки из преформ. Но, к сожалению, устойчивого резиноподобного состояния в разумно широком интервале температур удается достичь далеко не всегда (поз. 8 таблицы). Оценка "хорошо" для PP относится к новым специальным маркам, которые появились на рынке только недавно. В методе ЭР существуют приемы, позволяющие приблизиться к условиям метода ИВ и получить из одного и того же полимера бутылку более прочную, чем в обычном методе ЭР. Делается это так: на стадии "б" (рис. 1, а) зажатую в пресс-форме заготовку выдерживают некоторое строго установленное время, за которое она остывает до состояния, близкого к резиноподобному, и только затем раздувают. Таким образом удается из поливинилхлорида получить бутылку для газированных напитков. Следует особо рассмотреть особенности применения этого полимера.
PVC - полимер, имеющий хорошую прочность и хорошие барьерные свойства (см. таблицу). В него удается фасовать даже такие сложные для хранения продукты, как "живые йогурты", в которых сохраняются живые полезные бактерии. Эти бактерии боятся кислорода, а при их гибели продукт утрачивает свои полезные свойства. Но поливинилхлорид чрезвычайно вреден экологически. Его отходы нельзя сжигать, поскольку при сжигании PVC выделяются очень вредные вещества. Поэтому применение этого полимера в последние годы было запрещено в большинстве развитых стран, особенно для упаковки пищевых продуктов.
Запрет стимулировал поиск других технических решений. Выход был найден в разработке конструкций агрегатов для экструзионно-выдувного формования, позволяющих производить многослойные бутылки. Эти устройства снабжены не одним, а двумя или тремя экструдерами, которые одновременно подают разные расплавленные полимеры в трубную головку специальной конструкции так, чтоб трубная заготовка, а затем и бутылка получается многослойной. Снаружи и внутри трубной заготовки - слои недорогого полимера, который хорошо формуется в бутылку методом ЭР. Между ними располагается слой полимера с хорошими барьерными свойствами. Пример такой конструкции - бутылка для фасования высококачественных кетчупов. Несущие слои в такой бутылке изготовлены из полипропилена, барьерный слой - из полиамида.
Существует несколько способов выдува бутылок методом ЭР: сверху, снизу и сбоку иглой (рис. 2). Выбор того или иного способа определяется конструкцией бутылки, особенно горлышка, материалом, из которого изготовляется бутылка, особенностями выбранного пользователем выдувного агрегата. Способ выдува определяет, в свою очередь, конструкцию пресс-формы. Лучше всего эту работу проводить вместе со специалистами. Исходными данными для проекта являются: желаемая производительность, фасуемая жидкость, объем бутылки, способ заливки (горячая или холодная). После этого можно разработать дизайн и рабочий чертеж бутылки, а затем выбрать способ раздува и изготовить соответствующую пресс-форму.
Следует иметь в виду, что для производства бутылок методом экструзионно-выдувного формования необходим комплекс оборудования, но часто фирмы-продавцы лукавят, называя стоимость только отдельных машин для выдува. Кроме собственно выдувного агрегата необходимы сушилки сырья, холодильник для охлаждения экструдера и пресс-формы, дробилка отходов, устройство для замешивания технологических отходов с первичным сырьем.
Итак, метод экструзионно-выдувного формования бутылок переживает в России второе рождение. Это очень хорошо, что страна уже сейчас располагает специалистами в области проектирования, машиностроения и эксплуатации этих процессов.
Сабсай Отто Юльевич
Источник: http://www.sabsay.ru/articles/sabsay_2000_extrusion-blow-molding.htm
Читать другие статьи