Вспомогательное оборудование, применяемое при экструзионно-выдувном формовании
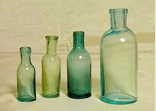
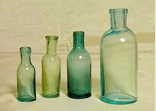
Целесообразность включение той или иной единицы вспомогательного оборудования в комплект поставки определяют по трём критериям:
- Техническая необходимость,
- Требуемый уровень автоматизации процесса,
- Экономическая целесообразность.
Ниже описано вспомогательное оборудование, применяемое при экструзионно-выдувном формовании полимерной тары и дан анализ целесообразности его применения, исходя из указанных критериев.
1. Компрессор
Без сжатого воздуха производство невозможно. Поэтому, если в месте размещения оборудования нет уже готовой линии высокого давления, необходима доукомплектация агрегата компрессором. Давление выдува зависит от формуемого материала и, как правило, не превышает 0.8 Мпа. Необходимый расход воздуха вычисляют как произведение обьёма бутылки и часовой производительности выдувного агрегата. Конечно, компрессорная станция должна включать ресивер и воздушные фильтры.
2. Холодильник
Охлаждения требуют три узла машины- пресс-формы, экструдер и гидропривод узла смыкания. Проточную воду из систем водоснабжения используют только на предельно примитивных кустарных производствах. Дело в том, что охлаждение пресс-формы - мощное средство регулирования технологического процесса и качества изделий. Скорость процесса- время охлаждения- очень слабая функция температуры охлаждающей воды. Она пропорцианальна натуральному логарифму разности исходной температуры изделия и температуры охлаждения. Однако, существует полуэмпирическое «правило вилки»: чем «резче» охлаждение, тем полимерное изделие твёрже и хрупче, и наоборот, - при медленном охлаждении изделие «мягкое» и минимально прочное.
В рассматриваемом случае это означает следующее. Если температура поверхности пресс-формы низкая, то внешняя поверхность бутылки твёрдая - устойчивая к царапанью и истиранию. Дальнейшее понижение температуры стенки формы приводит к охрупчиванию материала бутылки- при транспортировке , например, у таких бутылок отваливаются донышки. Рекомендуемая температура охлаждающей жидкости при переработке полиэтилена и полипропилена- 8град.С. Дальнейшее понижение температуры приводит к опасности выпадения росы на поверхности прессформы.
В конкурентной борьбе за качество изделий некоторые западные фирмы понижают температуру воды до трёх градусов и в этом случае кондиционируют зону формования сухим холодным воздухом. Для получения оптимально прочных, но не хрупких бутылок, контролируется и регулируется температура на поверхности пресс-формы вдоль оси рукава- заготовки. Конечно, вспомогательное оборудование типа специальных кондиционеров, пресс-форм специальной конструкции и датчиков-задатчиков температуры стенки формы устанавливают на полностью автоматизированных линиях большой мощности- с производительностью 2000 бутылок в час и более.
Скорость охлаждения прямо пропорциональна площади охлаждения и объемной скорости охлаждающей жидкости. Поэтому охлаждающие каналы в пресс-формах следует проектировать так, чтобы площадь контакта воды с охлаждаемой поверхностью была как можно больше. Не менее важно регулирование объемной скорости. Для этого холодильники снабжают мощными помпами. Рекомендуемое давление воды-0.4-0.6 МПа. Считается, что охлаждение хорошо отрегулировано, если разница температур на входе и на выходе холодильника составляет не более двух- трёх градусов. Необходимую холодопроизводительность системы охлаждения пресс-форм (кдж./час) можно оценить, умножив часовую производительность машины (кг/час) на 600 (для полиэтилена и полипропилена).
Представим себе, что зона загрузки экструдера, место, где шнек захватывает твёрдые гранулы полимера, не охлаждается. Тогда за счёт высокой теплопроводности металла шнек и корпус в зоне загрузки быстро нагреются до температуры превышающей температуру плавления полимера. Гранулы, попадая из бункера на эти горячие поверхности мгновенно подплавляются - образуется жидкая прослойка между самими гранулами и гранулами и рабочими поверхностями экструдера. В результате на входе в экструдер образуется вращающаяся пробка из подплавленных гранул, которую шнек не может протолкнуть дальше вдоль оси экструдера и которая не пускает новые порции холодных гранул в зону загрузки. Технологи говорят: «пропадает насосный эффект пары шнек- цилиндр». Для таких полимеров, как полиэтилен и полипропилен, охлаждение зоны загрузки обязательно, а, когда перерабатывают полистирол на машинах большой мощности, как правило, применяют ещё и специальные шнеки с охлаждаемой внутренней полостью.
В «горячих» зонах экструдера температура поддерживается мощными электронагревателями. Инерционность этих устройств велика и, поэтому, на хороших машинах в каждой «горячей» зоне устанавливают либо воздушные вентиляторы, либо предусматривают водяное охлаждение, либо применяют и то и другое вместе. Этим достигается точное задание и поддержание необходимых температурных режимов в каждой зоне подогрева экструзионной машины.
Для всей системы охлаждения экструдера достаточно воды с температурой 25 град.С. Такая же температура достаточна для охлаждения масла гидросистемы узла смыкания пресс-форм.
3. Сушилки
Полиэтилен мало гигроскопичен. Достаточно хранить сырьё в отапливаемых помещениях при относительной влажности воздуха не выше 4 градусов точки росы. Качественная переработка других полимеров невозможна без подсушки сырья. Полимер рассыпают на поддон тонким слоем и помещают в термошкаф. Время выдержки и температура, разные для разных термопластов. На высоко автоматизированных крупнотоннажных производствах полимеры сушат, продувая через них горячий воздух. В случае переработки полиэтилентерефталата обязательна предварительная подсушка воздуха в адсорберах.
4. Дозаторы для замешивания красителей
Как правило, красители добавляют в полимеры в форме заранее приготовленных на специализированных предприятиях гранулированных маточных смесей собственно полимера и красителя (masterbatch); для окрашивания ПЭ - с ПЭ, для окрашивания РЕТ - с РЕТ и т. п. При этом гранулы концентрата в пределах допусков должны иметь те же размеры и массу, что и гранулы перерабатываемого полимера. В противном случае из- за неодинаковых условий плавления в зоне загрузки экструдера будут происходить нежелательные явления, описанные в разделе 2. Количество красителя в этих концентратах, как правило, колеблется в пределах от 10 до 30% (вес.), а добавляют концентраты в базовый полимер при переработке в количествах порядка 1% (вес.). Понятно, что при таких малых концентрациях собственно красителя. малейшее изменение дозы приводит к изменению интенсивности окрашивания, хорошо заметному невооружённым глазом. Меняется также и однородность окрашивания отдельного изделия.
Простейшим приёмом дозирования красителей является следующий: Базовый полимер и краситель отдельно завешивают на весах в нужной пропорции. Затем ингредиенты соединяют и перемешивают. Как правило, для этого применяют самодельные смесители «Пъяная бочка». Это ёмкость цилиндрической или прямоугольной формы с осью вращения, расположенной под углом к главной геометрической оси ёмкости. Смесь загружают в устройство, загрузочный люк задраивают, и в ручную, или с помощью привода вращают в течение 5-10 минут. Такой приём дозирования распространён в России на производствах малой мощности. В западных странах, даже для малотоннажных процессов применяются специальные дозаторы:
Базовое сырьё из силоса или любой другой промежуточной ёмкости, дозированно с постоянной скоростью подают в бункер экструдера с помощью гибких шнековых транспортёров. Скорость подачи регулируется путём изменения числа оборотов шнека. Иногда применяют и плоские транспортёры или дискретную подачу пневмотранспортом так, чтобы сыръё подавалось постоянно маленькими заданными порциями. Над бункером экструдера закрепляют маленький дозатор красителя. Это простейшее устройство представляет собой бункер (как правило, загрузки хватает на 8 часов работы) и подающее устройство. Устройств, в основном, два:
- Шнек с регулируемой скоростью вращения - шнековый дозатор и
- Вибродозатор- лоток с регулируемым углом наклона относительно горизонта и эксцентриковым или индукционным виброприводом. Такой способ позволяет наиболее точно и равномерно дозировать красители. Более того, его реализация не намного дороже, чем стоимость весового оборудования и мешалок. Важным дополнительным преимуществом, конечно, является автоматизация процесса.
Иногда в бункер экструдера дополнительно встраивают лопастную мешалку или широкий шнек, который транспортирует смесь снизу верх- смесь под собственным весом снова осыпается вниз и т. д.
5. Обрезка отходов
При производстве бутылок методом экструзионно-выдувного формования всегда есть промышленные отходы. Это не брак. Просто такова особенность этой технологии. В случае, когда выдувают дорном сверху или снизу теоретически обрезки экструдата отделяются от сформованной бутылки сами собой, когда бутылка остывает и падает в накопитель. На практике, особенно при переработке полиэтилена, этого не происходит. Поэтому процесс отделения отходов специально автоматизируют.
Устройств множество - это и специальные захваты, отрывающие отход около дна бутылки («Ходос»), и более сложные захваты транспортёры («Бекум»). Для условий России при производительностях порядка 500 бутылок в час можно рекомендовать отрывать отходы в ручную, поскольку, как правило, все эти устройства дороги и ненадёжны.
В случае, когда бутылку выдувают иглой, в технологии обязательно присутствует отход со стороны горлышка, который обрезается специальными вращающимися ножами. В простейшем случае такие устройства обрезки выполняются в виде отдельной машины. Бутылки для обрезки вставляют в эту машину в ручную. В дорогих, высокоавтоматизированных агрегатах («Крупп», «Бекум») предусмотрены специальные транспортёры- захваты, подающие готовое изделие в устройство обрезки. Для «жёстких» материалов, таких как поливинилхлорид, фирмой «АДС» разработана специальная конструкция прессформы со встроенным обрезным ножом. Количество отходов зависит от способа выдува и от сложности конфигурации бутылки и может достигать 30-40% от общего веса потребляемого сырья. Процесс считается конструктивно правильно построенным, если общее количество отходов не превышает 15%.
6. Устройства утилизации отходов
Конечно, на дорогостоящих крупнотоннажных производствах отходы автоматически отделяют от готовых бутылок, дробят, смешивают с первичным сырьём и пускают снова в производство. Добавлять «вторичное» сырьё в «первичное» всегда плохо. Допускают, что без значимого ущерба для качества изделий возможна добавка 15-20% (вес.) отходов в основной процесс. В настоящее время существует множество фирм, скупающих вторичное сырьё и применяющих его для производства неответственных изделий технического назначения, например, закладных труб для прокладки электрокабелей. Поэтому, когда выпускаются изделия ответственного назначения, такие, как бутылки, иногда выгодно продавать отходы, а не пускать их снова в производство.
Тем не менее, рассмотрим подробно процесс утилизации отходов в основное производство.
Дробят отходы в специальных устройствах- дробилках. Дробилка состоит из корпуса в котором установлены вращающийся ротор с закреплёнными на нём твёрдыми ножами и неподвижные ножи- статор. Снизу корпуса закреплена сетка с ячейками заданной величины. Через ячейки падают в нижнюю ёмкость дроблёные отходы. Как видно из описания цель устройства- довести величину отходов до размеров близких к размерам гранул, чтобы их можно было бы хорошо перемешать и загрузить в экструдер. Отходы не должны быть слишком мелкими и содержать много пыли, чтобы в зоне загрузки не образовалась пробка. Величина диаметра ячейки сетки при дроблении полиэтилена составляет 6- 8мм.
Дроблёные отходы либо продают (конечно, они стоят дороже), либо завешивают, смешивают с первичным сырьём и подают в бункер экструдера. Как бы качественно не была подготовлена смесь- всё равно остаётся опасность образования пробки и зависания смеси в бункере (образование свода). Для того, чтобы избежать этих нежелательных явлений, применяют по крайней мере два приёма:
- В бункере литьевой машины устанавливают дополнительный шнек, который уже действует не как в предыдущем случае снизу вверх, а создаёт дополнительный подпор сверху вниз.
- В зоне загрузки экструдера устанавливают рифлёную втулку, увеличивающую сцепление гранул с корпусом цилиндра.
Сабсай Отто Юльевич
Источник: http://www.sabsay.ru/articles/sabsay_2002_auxiliary.htm
Читать другие статьи